Next Generation Innovation for a New Decade
March 03, 2020 by Zina ZhuMilliken’s focus on R&D innovation is driving the development of next generation plastics and packaging that improve people’s lives and transform the impact of plastics on the environment for the better. In recognition of this, and in a great way to kick-off Milliken’s next decade of innovation, we were recently the product recipient of the SIES SOP Star Award for excellence in packaging for our primary product packaging based on a clarified random copolymer.
This ultra-high clarity package, made from polypropylene (PP), for a liquid detergent/cleaner, has a 4th generation clarifier, using extrusion blow molding technology, and comes with a special ‘no break’ grade. Features of the clarified random copolymer, such as ultra-high clarity and gloss, high shelf appeal, better chemical resistance, reduced product weight due to low density, being re-usable and recyclable, help brand owners to create a new market space for themselves by shifting from conventional HDPE to ultra-high clearer packaging.
The SIES School of Packaging in Mumbai started the SIES SOP Star Awards in 2017 with an emphasis on innovation, creativity and new concepts and, in 2019, experts in a variety of fields relating to packaging chose Milliken as a worthy winner in the category of ‘Plastics - Rigid Packaging’.
To add to the product attributes, the polypropylene used is an environmentally-friendly material with low carbon footprint during its manufacturing, and recyclability with high energy recovery values.
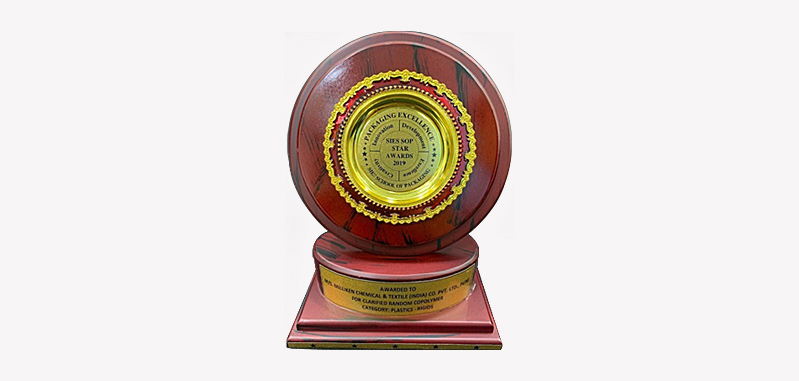
Beyond Awards – Milliken Innovation in Action
Also in the innovation and sustainability spotlight is Milliken’s Millad® NX® 8000 clarifying additive, used to produce the fully transparent material known as NX® UltraClear™ PP, which yields durable end products with superb, glass-like clarity. This makes PP a viable alternative to resins such as PET and polystyrene in a wide range of packaging applications.
Many bottles and containers today rely on multilayer constructions using a variety of materials to deliver the end package which may produce the necessary product performance but can be bad for the environment. Known as multi-material packaging, this often hinders recyclability. In many applications, PP can be used not only in the bottles but also in the caps and labels, offering a viable, mono-material solution that doesn’t require adhesives or glues.
By enabling clear, transparent, Millad NX 8000-modified PP to replace alternative materials, brand owners and converters improve their options for producing more recyclable, mono-material products, for example, bottles or containers, plus their labels and caps all in PP, enhancing recycling.
Another forward looking product is Milliken’s Hyperform HPN-900ei for thin wall injection molding. This additive gives PP unique physical properties that balance bi-directional stiffness and impact resistance, while allowing for highly tuned resin systems that meet high shrinkage and thermal performance tolerances.
Both Millad NX 8000 and the family of Hyperform HPN performance additives for PP offer significant environmental benefits and have been awarded the prestigious UL certification. Millad NX 8000 clarifier for polypropylene was the first Milliken product to gain energy savings-related certification from UL whilst four grades of Hyperform HPN are recognized as enabling an average of 5-8 percent energy savings for firms that injection mold thin-wall container lids or similar PP products.
Continuing this innovation for customers, Milliken plans to pursue UL certification for additional nucleators in various applications, including for other processes such as thermoforming.
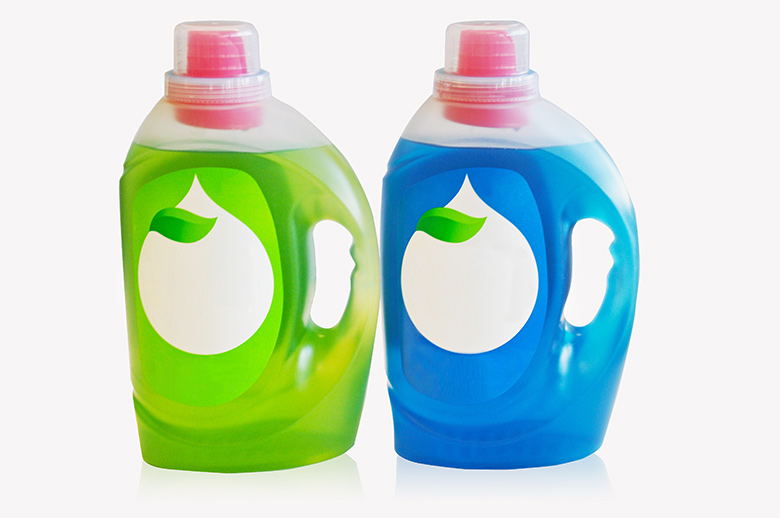
Collaboration for Innovation
For many innovations collaboration is key. In this regard, Milliken is proud of its partnership with PureCycle Technologies to restore used polypropylene plastic to 'virgin-like' quality with a revolutionary recycling method. PureCycle’s patented recycling process, developed and licensed by P&G, separates color, odor and other contaminants from plastic waste feedstock to transform it into virgin-like resin.
Today, about 20 percent of polyethylene terephthalate (PET), which is commonly used to make plastic bottles and other consumer goods, is recycled. By contrast, less than 10 percent of polypropylene plastic is currently recycled. PureCycle is the first company to solely focus on recycling and reintegrating polypropylene upstream to highly sensitive consumer product applications, which are used in food and beverage and consumer goods packaging, automobile interiors, electronics, home furnishings, and many other products.
This beyond concept method will enable the recycled material to become truly circular, and be reused in its original application, as opposed to having to be downcycled into lower-value products, and Milliken’s additives will play a critical role.
Looking ahead to the 2020’s
As we enter a new decade, the world is at the beginning of a more sustainable, and innovative, future. As we evolve our new ideas and technologies, Milliken will continue to provide new solutions to help customers become more sustainable with better packaging for a brighter future.