Enhancing Plastics with Performance
October 07, 2019 by Emily BlairEverybody wants plastic additives that result in faster, more efficient production, improved stiffness properties, superior protection from the sun’s UV rays and great aesthetics, and Milliken’s next-generation additives are doing just this.
In addition, as the industry moves towards a circular economy, these sustainable technological innovations that enhance the performance of plastics, boost productivity and maintain balance, are supporting these sustainability efforts. K 2019 is a showcase for Milliken’s next-generation additives that improve the performance of the polymers they modify, helping to, for example, extend the shelf life of packaged materials to enabling the construction of stronger, lighter parts.
Additives for enhanced performance and sustainability
One of Milliken’s R&D areas of focus is helping to develop products that boost performance and aesthetic properties. This is important because helping end-products to keep their high-quality finish for longer reduces the chances of being disposed of prematurely, contributing to sustainability. Several Milliken additives on display at K 2019 serve to improve the performance of the polymers they modify.
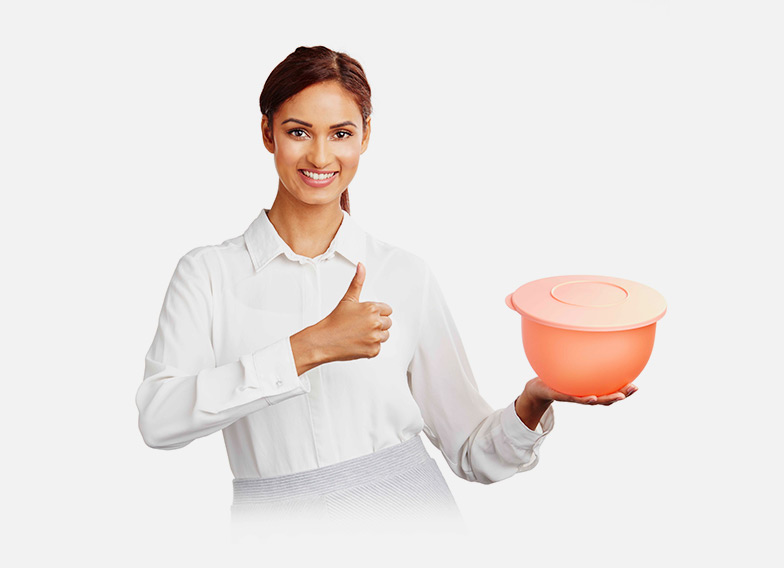
Hyperform® HPN™ performance additives for polypropylene (PP) are game-changing, embracing the key sustainability- and performance- related challenges affecting today’s plastics processing industry by enabling lightweighting, while also enhancing productivity and optimizing processing. Easy to use and reliable, Hyperform HPN maximizes the performance of PP by reducing productivity problems.
Adding Hyperform® HPN™ performance additives to polypropylene increases the crystallization temperature and the rate of crystallization. This benefits users by reducing both cooling time and cycle time, which results in higher processing productivity. In fact, Milliken Hyperform HPN products enable 5% to 8% energy savings when used as a nucleator in the production of thin-wall injection molded container lids or similar polypropylene products. UL Environment & Sustainability’s verification services have assessed several grades of the Hyperform additive and all earned recognition for their energy-related sustainability performance.
Traditional nucleating agents often increase stiffness at the expense of impact strength. Hyperform HPN performance additives, however, strike a key performance balance by improving stiffness while retaining the same impact behavior. This enables the production of stronger, thinner parts, and promotes stability at high temperatures.
Hyperform HPN performance additives also promote isotropic shrinkage, which improves dimensional stability and reduces part warpage. This, in turn, enhances final part quality, limits waste and contributes to faster, more efficient processing.
And last but not least pigments add vital color but their impact on PP formulations can make it difficult to mold parts with identical dimensions and may contribute to increased part warpage. Hyperform HPN performance additives override the nucleation effect of pigments, allowing converters to produce a variety of colored parts with identical dimensions in the same mold. This simplifies processing and design since only one set of production conditions is needed for various colors.
At K 2019, Milliken will be introducing its latest grade, Hyperform HPN-715, offering new opportunities for PP to replace more-expensive engineering resins in demanding applications. The performance additive enables downgauging and reduces filler requirements to improve design freedom, reduce weight and cut material costs. Hyperform HPN-715 delivers an optimized balance of various key factors, while also providing higher heat-deflection temperatures compared to other advanced performance additives This allows PP to be used in microwaveable containers, under-hood vehicle components and in household appliance parts.
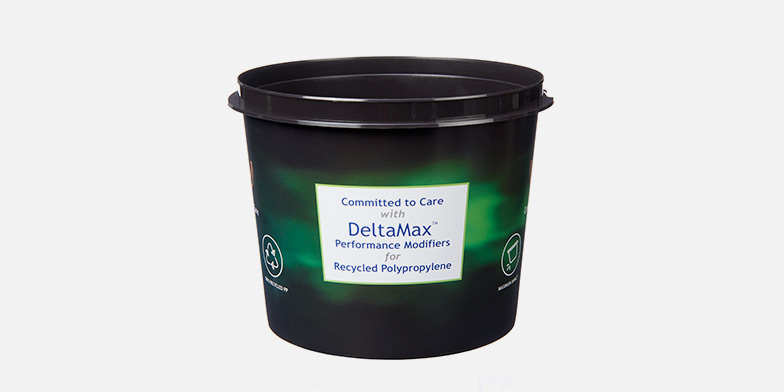
Also at K 2019 converters can discover how Milliken’s DeltaMax™ Performance Modifiers for PP enhance the impact strength and flow properties of polypropylene impact copolymers (ICPs), blends and recycled polypropylene (rPP) resins. The DeltaMax modifiers are used to expand the physical performances, and improve the efficiencies of, making impact copolymer resins. This allows converters to increase operating efficiencies and create more innovative part designs with easier flow through molds.
DeltaMax technology is also effective in modifying post-consumer and post-industrial recycled resins. It elevates melt flow without sacrificing impact properties, allowing recyclers to source a wider variety of feedstocks and expand their product offerings. This enables compounders and converters to incorporate higher amounts of recycled PP without sacrificing performance or processing.
“DeltaMax solves a long-standing unmet need in the polypropylene industry,” said Emily Blair, Milliken’s global product line manager. “Converters, brand owners and OEMs can now make superior designs and more durable products while keeping a keen eye on improving sustainability and costs.”
At the K show, Milliken also plans to introduce the latest addition to its DeltaMax family.
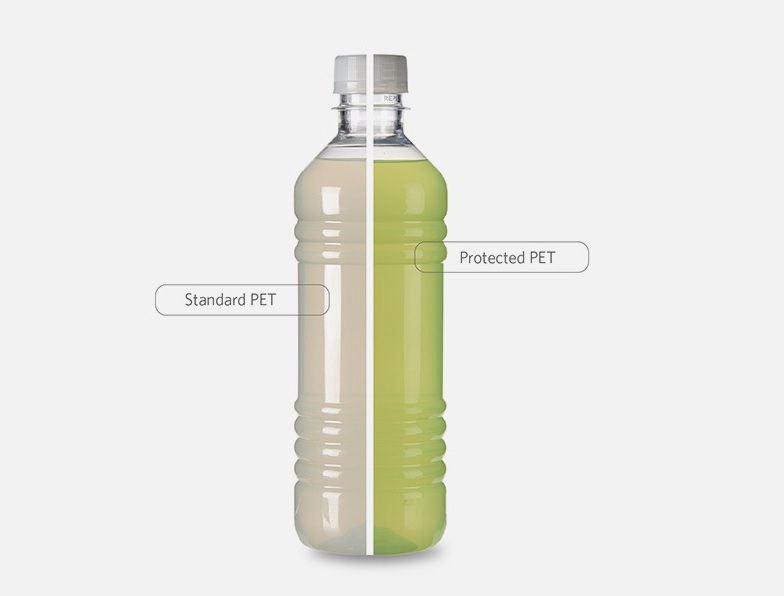
Finally, our ClearShield™ UV Absorber gives the ultimate protection from damaging UV light to PET packaged materials such as food, beverages and consumer products. This technology creates a new UV protection performance standard, offering an efficient way to protect against exposure to harmful ultraviolet light by incorporating the UV absorber into the PET package itself.
PET modified with ClearShield is a simple, cost-effective alternative that is approved for food contact. It doesn’t require any changes to product formulation and maintains the clarity of the packaging. ClearShield allows the storage and display of products in crystal-clear packaging, extending the shelf life of packaged materials, protecting brand image and allowing more sustainable formulations with natural colorants, flavors and essences.
Looking to the future
“Our promise is to deliver plastic additives that result in faster, more efficient production, improved part stiffness, excellent UV protection and superior aesthetics,” said Herrin Hood, global marketing director of Milliken’s Plastics Additives business. “At the same time, these products will help create a more sustainable plastics industry as we move towards a circular economy and work to create a positive impact on the world.”
On display at K2019 are our additives, colorants and other products that help to take our industry closer to a circular economy. Visit our booth (Hall 6/A27) to find out more about these, particularly our game-changing plastics performance additives - Hyperform® HPN™ nucleating agents, DeltaMax™ Performance Modifiers and our ClearShield™ UV Absorber.